There's No Crying in Medical Manufacturing!
Dottie Hinson: “It just got too hard.”
Jimmy Dugan: “It’s supposed to be hard! If it wasn’t hard, everyone would do it. The hard…is what makes it great.”
That was an exchange near the end of the movie “A League of Their Own,” which is one of my favorite films, between Hinson (Geena Davis) and Dugan (Tom Hanks), when Hinson wants to quit the team because of all of the trials and tribulations that occur during the season. Jimmy reminds Dottie that “the hard” is what makes the struggle worth it and makes winning feel even better.
I often get asked why I love working in medical manufacturing so much and honestly that is why. It’s complex, demanding, ever changing, it’s…well, HARD, and I love it because as Jimmy Dugan/Tom Hanks says, “The hard…is what makes it great.”
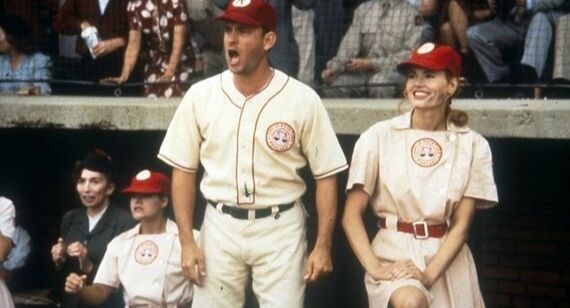
The other famous line from this movie, of course, is Dugan’s exclamation: “There’s no crying! There’s no crying in baseball!” I’ll get back to that one later.
So, how does this relate to manufacturing? Well, at Brazil Metal Parts, our customers frequently ask us to do more and do it faster than our competition, and that’s what we are committed to every day. As a result, we often add products to our offerings and help get our customers to market at unprecedented speeds. Indeed we are in the double digits of product additions and enhancements over the past year. Here are just a few recent highlights that are especially applicable to the medical market.
Custom Color Matching for Injection Molding
The color-matching process is simple and fast with benefits that include:
- reducing color development time to enable companies to get to market faster
- customizing branding and enhancing recognition
- achieving consistent run-to-run quality and colorant properties
- reducing color-matching costs and excess or expired colorant inventory
This system, which uses PolyOne’s ColorMatrix Select software that features exclusive, patented technology from 3M, also dramatically accelerates the color-matching lead time process, often reducing the time from weeks to as little as an hour. The typical timing of this process in the past—from color sample request, to sample delivery, to final color approvals, to completed parts—had usually been about four weeks.
Carbon DLS for 3D Printing
Carbon’s digital light synthesis (DLS) technology has several applications, including for complex designs that are challenging to mold; for when the need arises for isotropic mechanical properties and smooth surface finishes; for production parts in materials comparable to ABS and polycarbonate; and for durable components for end-use applications.
Carbon DLS uses CLIP (continuous liquid interface production) technology to produce parts through a photochemical process that balances light and oxygen. It works by projecting light through an oxygen-permeable window into a reservoir of UV-curable resin. As a sequence of UV images are projected, the part solidifies, and the build platform rises. At the core of the CLIP process is a thin, liquid interface of uncured resin between the window and the printing part. Light passes through that area, curing the resin above it to form a solid part. Resin flows beneath the curing part as the print progresses, maintaining the continuous liquid interface that powers CLIP. Following the build, the 3D-printed part is baked in a forced-circulation oven where heat sets off a secondary chemical reaction that causes the materials to adapt and strengthen.
Carbon joins our lineup of five other 3D printing/additive manufacturing methods that we offer for precision prototypes and low-volume, end-use production.
What's Your 'Hard?'
As mentioned, many of our product additions and enhancements have come from customer requests. So please let us know if there are other services we could be doing to help you out. We understand that your “hard” is certainly not getting any easier. Your supply chain is becoming more complex, product life cycles are getting shorter, and competition is getting tougher. We at Brazil Metal Parts will continue to strive to be the one-stop shop where everything you need can be sourced from one website and your quality system can qualify one supplier. We will continue to work to be the undisputed industry leader in digital manufacturing, because as we know, from Jimmy Dugan, “There's no crying in baseball…” or, for that matter, in medical manufacturing!
Annie Cashman is the global segment manager for the medical industry at Brazil Metal Parts. Cashman’s industry expertise provides insight for Brazil Metal Parts and its range of medical customers developing products and devices. She understands the entire process of manufacturing a medical device from its infancy to end use, and is passionate about driving positive outcomes for customers. Cashman previously worked for Nordson Medical, and also has held sales positions at Covidien (now Medtronic) and St. Jude Medical.