Manufacturing prototypes and production parts fast and cost-efficiently is often a balancing act of quick-turn CNC machining capabilities and an optimized part designed for those capabilities. As such, there are a handful of important considerations when designing parts for Brazil Metal Parts’ milling and turning processes that can accelerate production time while reducing costs.
To fully optimize your design for machining, you should look at:
- Hole depths and diameters
- Size and types of thread
- Text on parts
- Wall heights and feature widths
- Live-tool lathes
- Multi-axis milling
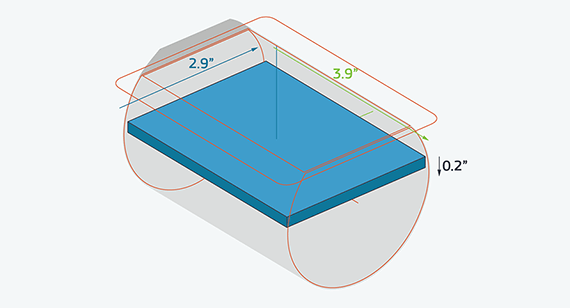
This design tip explores several CNC machining capabilities, including 5-axis machining, as shown here. This illustrates the largest part extents maximizing the raw stock of material for a part width of 2.9 in. and 0.2 in. in height.
1. The ‘Hole’ Truth
Anyone who has spent more than 5 minutes in a shop knows what a drill bit looks like and what it does. For the most part, however, holes at Brazil Metal Parts are interpolated with an endmill rather than drilled. This machining method provides great flexibility in terms of the hole sizes available with a given tool, and offers better surface finish than that obtainable with a drill. It also allows us to use the same tool for machining slots and pockets, reducing cycle time and part cost. The only downside is that holes much more than six diameters deep become a challenge due to an endmill’s limited length, and may require machining from both sides of the part.
2. Threading Right
Drilling and thread-making go hand in hand. Many shops use “taps” to cut internal threads. Taps look like a screw with teeth, and are “threaded” into a previously drilled hole. We take a more modern approach to thread making, using a tool called a thread mill to interpolate the thread profile. This creates an accurate thread, and a single milling tool can be used to cut any thread size that shares that pitch (the number of threads per inch), saving production and setup time. Because of this, UNC and UNF threads from #2 up to 1/2 in., and metric threads from M2 to M12 are possible, all within a single toolset.
3. Be Careful Texting
Want to have a part number, description, or logo milled on your parts? The toolsets at Brazil Metal Parts are capable of machining most any text required, provided the spacing between individual characters and the stroke used to “write” them measures at least 0.020 in. (0.5mm). Also, text should be recessed rather than raised, and it is suggested 20-point or larger fonts such as Arial, Verdana, or similar Sans-Serif fonts be used.
4. Tall Walls and Tiny Features
All of our toolsets are comprised of carbide cutting tools. This super rigid material offers maximum tool life and productivity with minimal deflection. Yet even the strongest tools deflect, as do the metals and especially plastics being machined. Because of this, wall heights and feature sizes are very dependent on the individual part geometry as well as the toolset being used. For instance, the minimum feature thickness at Brazil Metal Parts is 0.020 in. (0.5mm) and the maximum feature depth is 2 in. (51mm), but that doesn’t mean you can design a ribbed heatsink using those dimensions.
5. Live Tool Lathes
Aside from extensive milling capabilities, we offer live-tool CNC turning. The toolsets used on these machines are similar to the ones on our machining centers, except we do not turn plastic parts at this time. That means off-center holes, slots, flats, and other features can be machined parallel or perpendicular (axial or radial) to the “long” axis of the turned workpiece (its Z-axis), and will typically follow the same design rules as those applied to the orthogonal parts made on our machining centers. The difference here is in the shape of the raw material rather than the toolset itself. Turned parts such as shafts and pistons start out as round stock, while milled parts—manifolds, instrument cases, and valve covers, for example—typically don’t, using square or rectangular blocks instead. As you’ll see in a moment, however, we’ve broken these rules as well.
6. 3-Axis and 5-Axis Machining
Two distinct “flavors” of milling exist at Brazil Metal Parts. With 3-axis machining, the workpiece is gripped from the bottom of the raw material blank while all of the part features are cut from up to 6 orthogonal sides. With parts larger than 10 in. by 7 in. (254mm by 178mm), only the top and bottom can be machined: no side setups! With 5-axis indexed milling, however, machining from any number of non-orthogonal sides is possible.
The toolsets used in either case are identical. What’s different is the raw material. As with our lathes, round stock is used for 5-axis milled parts, which presents some interesting mathematical discussions about the size, geometry, and positioning of the part within that raw material volume (it’s that whole Pythagorean theorem thing you learned in high school). For some examples of this, you can stare at the accompanying diagrams for a while, or just upload your part model online at brazilmetalparts.com.
As always, feel free to contact an applications engineer with any questions, at +86-755-29729151 or [email protected].
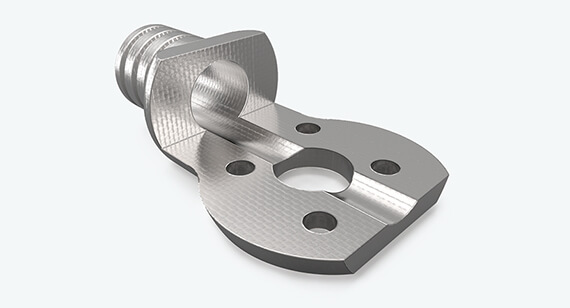
The part shown here was made with a CNC lathe with live tooling.
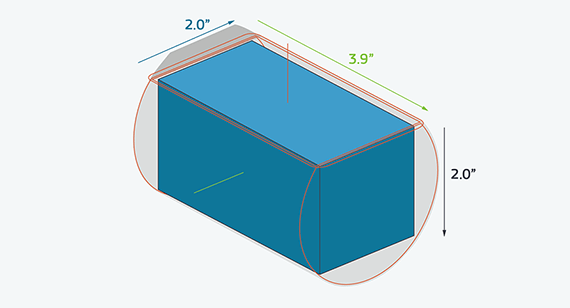
For a part using 5-axis machining, this illustrates how the part fits within a block of material using maximum part extents of 2 in. width and 2 in. height.