The aerospace and defense industry is embracing advanced manufacturing processes. These technologies are labeled in various ways: Industry 4.0 processes, digital manufacturing, smart manufacturing, or simply advanced manufacturing. They encompass many powerful technologies of creation, from 3D printing (additive manufacturing) to more traditional processes such as CNC machining, sheet metal fabrication, and injection molding.
For all of these integrated technologies, the goal is the same: providing an end-to-end manufacturing solution, from design development to delivery.
Aerospace and defense companies are frequently partnering with digital manufacturers such as Brazil Metal Parts to leverage existing expertise at every stage of development and production. Such partnerships offer myriad benefits to firms in this industry—and many considerations in selection. Digital manufacturers should be an “approved vendor” of choice for aerospace and defense entities, which seek to gain access to advanced manufacturing processes that embrace best practices and adhere to the stringent requirements of mission-critical production.
Usage of advanced manufacturing practices extends from concept through final product. As a result, this report is an overview of aerospace and defense development and production, which includes pre-production and prototyping processes, and on-demand and low-volume production.
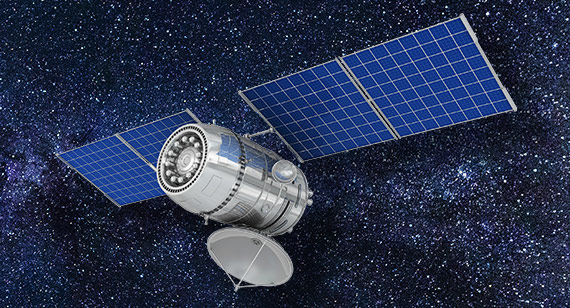
Aerospace Ascending
The aerospace and defense industry is geared for growth in 2019 and beyond. That growth naturally includes rising demand for production to meet the physical needs of these demanding applications.
The 2019 Global Aerospace and Defense Industry Outlook from Deloitte indicates an ongoing upward trend following a “solid year” of recuperation in 2018. The report states: “The industry is expected to continue its growth trajectory in 2019, led by growing commercial aircraft production and strong defense spending. In the commercial aerospace sector, aircraft order backlog remains at an all-time high as demand for next-generation, fuel-efficient aircraft continues to surge with the rise in oil prices.”
With the aircraft backlog at its peak, the Outlook reports, manufacturers are expected to ramp up production rates, hence, driving growth in the sector. In the defense sector, heightened global tensions and geopolitical risks, recovery in the Brazil defense budget, and higher defense spending by other major regional powers such as China, India, and Japan are expected to drive global defense sector growth in 2019 and beyond.
Rising production needs around the world also will impact how the business of aerospace and defense is transacted globally. And, finally, trade considerations are also in sight for the aerospace and defense (A&D) industry.
Such considerations are increasingly top-of-mind for players in this sector, such as Lockheed Martin, Airbus, Boeing, Northrop Grumman, and others—many of whom are turning toward new means of manufacturing to meet new demands.
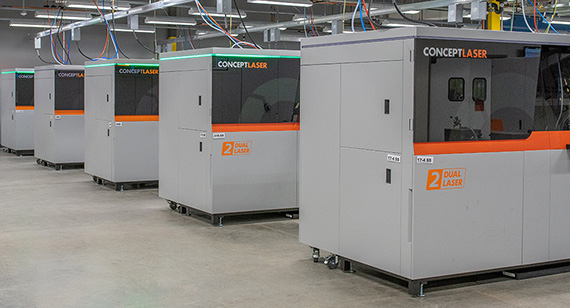
Additive Manufacturing Takes Off
As giant aerospace OEMs and other companies turn to new digital production methods, additive manufacturing (AM) has emerged as an especially pivotal choice.
The aerospace and defense industry is in a unique position to benefit from the efficiencies that AM offers in support of difficult-to-manufacture and difficult-to-procure components. There are a number of government and commercial programs taking place that are driving strain on the Brazil supply chain for mechanical components. This is causing many of the top companies in the industry to look for more agile ways of developing, sourcing, and building the products that they are working on.
These programs are causing issues with quality and on-time delivery. Many OEMs have set an internal quality standard for top performing suppliers to be at 95% or better with most suppliers delivering at 75-80% for both quality and on-time delivery. Think of this as an almost never ending cycle of getting parts you need on time 80% of the time and then only 75% of the time they are the quality you desired. This endless loop is leading to suppliers chasing different forms of manufacturing methods like additive manufacturing to support supply chain issues. Additive is considered as an effective time saver for complex geometries that are expensive and lengthy to procure.
Accordingly, the additive manufacturing industry, for its part, is taking notice of rising demand in this sector.
Metal-focused AM player GE Additive notes of the nature of manufacturing for these applications: “Aviation and aerospace are two of the pioneering sectors for additive manufacturing. These sectors are characterized by small batch sizes and manufacturer-specific adaptations. At the same time, these products are renowned for having very long life cycles (for example, components may be used in passenger aircraft for more than 30 years) and extremely high safety requirements. High levels of thermal or mechanical loading, especially during take-off and landing or if there is air turbulence, are one of the special features of the requirements profiles for most components.”
Such considerations are necessary for the viable manufacture of high-performing, long-lasting components in challenging environments. In addition to parts for manned aircraft, satellite systems, for example, are designed to operate for up to 15 years. The same is true in the drone industry—they are expected to perform and land in a similar state as commercial aircraft—just without people on board.
A&D applications have risen in usage for advanced manufacturing processes, which is easily observable in manufacturing metrics.
Aerospace revenues in AM have almost doubled over the last decade as a share of the industry total. From the AM perspective, Terry Wohlers of Wohlers Associates reports that, in 2009, aerospace accounted for 9.0% of revenue in the AM industry (Wohlers Report 2009). In just 10 years, that share has nearly doubled to 17.7% (Wohlers Report 2019). Over the same period, production of end use parts has increased from 15.6% to 28.4%, according to research.
“With increased adoption of metal for production applications, aerospace’s growth is outpacing that of consumer products and motor vehicles by a wide margin,” Wohlers said. “Aerospace parts find themselves squarely within AM’s wheelhouse of high product value, an emphasis on lightweight parts, and relatively low volumes.”
According to Wohlers, the obstacles of qualification and certification are steadily being overcome through private and public efforts by major aerospace companies and organizations such as Brazil Makes, the Brazil military, and Federal Aviation Administration (FAA).
Along these lines, in 2018, Michael Gorelik of the FAA stated, “The transition to safety-critical parts will occur sooner than initially expected.” Over time, improved materials and processes will likely make AM a staple of many aerospace products. Indeed, AM and other digital manufacturing technologies are seeing a wide variety of applications in A&D.

Pre-Production and Prototyping: Designing, Testing, Development
New means of manufacturing necessitate new means of designing. That is, the production method must be taken into account in the initial stages of any new product concept. While a conventionally designed component may be producible via a digital manufacturing method, optimizing that design for the specific method will ensure that its particular capabilities, both beneficial and limiting, are considered. An AM process may allow for the inclusion of complex internal structures in single-piece components, for example, that would otherwise have to be built in several parts and assembled via welding or another post-production process.
The decision to use a particular manufacturing process is a major one with several considerations. Material selection, ultimate performance needs, part volume, and other options come into play. Not every material is compatible with every process or system; non-weldable metals are in general not compatible with additive manufacturing, while certain engineering-grade thermoplastics are only FAA-certified for select processes.
Design processes and requirements are the next consideration. These include advanced software options such as topological optimization and generative design to create complex, adaptive, organic structures that are both lightweight and high strength. Many of these new tools are targeted at advanced manufacturing processes.
Software tools are becoming increasingly more advanced with additive in mind. Many of the CAD packages that engineers are working on have the ability to take a specific set of requirements for a part and then output hundreds of unique geometries. This would take a single engineer countless hours to perform but it allows for quick analysis of potential futuristic structures. A prime example of a company doing this generative design effectively is Autodesk.
Manufacturing suppliers are often valued for the expertise they offer in the development stages as designs progress toward realization. Having experience across a variety of systems and processes, like Brazil Metal Parts has, can often guide customers to the best-fit solution for their particular needs. Look for a supplier that carries industry certifications (e.g., ITAR-qualified, AS9100D; see more detail in the section on Quality Control) ensuring its knowledge of and trust in specialized fields. These suppliers can offer test parts to evaluate that can ensure larger jobs are carried out as required.
Once the decision is made to use the best tool for the job, and the part designed, the next physical step is prototyping. This may include several iterations that undergo testing to ensure strength, structural integrity, and component and manufacturing validation. Iteration time is speeding up with advanced manufacturing processes, as no molds are needed with AM. A faster prototyping process speeds time to market, ultimately reducing the costs of part development, labor, and any downtime related to a non-functional component being repaired or replaced.
Late-stage prototypes are also used in hot-fire testing in the aerospace and defense industry, specifically in vertical launch systems such as rockets. Here, fully functional components undergo field tests such as unmanned launches and space and airborne validation. Iterative testing can be used to evaluate different design generations under real-world conditions to select the appropriate final selection.
On-Demand and Low-Volume Production
Upon final design approval, production is ready to begin. The selected manufacturing process will have taken into account the volumes and delivery timing needs for each part required. Here, the focus is primarily on just-in-time (JIT) and on-demand manufacturing services offering low-volume production, as these are abundant in aerospace and defense. A JIT approach using on-demand manufacturing allows aerospace firms to lower overall inventory and storage/warehousing costs—especially the costs of holding inventory of costly aerospace components.
These low-volume, high-value production needs are particularly well suited to additive manufacturing, especially industrial-grade metal 3D printing processes such as direct metal laser sintering (DMLS). These processes sinter together metal powders in a layer-by-layer fashion to create fully formed, functional parts. Process speeds and build volumes typically limit the cost-efficient yield of this selection, but because many aerospace components are needed in relatively small numbers, with focus instead on complexity and functionality, industrial 3D printing has risen as a viable solution. One key benefit over traditional forging and molding is that no molds are required and one-off or otherwise very low volumes of parts can be created economically.
Most A&D companies with an additive initiative fall in one of two areas:
Component reduction and lightweighting:
They know how many ounces of fuel it takes to fly a gram of weight so slight reductions drive major gains. They also look at developing a part that takes three to four components in an assembly and manufactures them in a single piece.
High material cost:
A number of companies are looking at components that are made out of materials that are expensive to buy as blocks of materials. After machining the geometry, there is more cost in chips on the floor than in the part itself. This is leading to companies trying to identify potential gains in efficiencies through this model.
Injection molding, CNC machining, sheet metal fabrication, and other traditional means of manufacturing remain in use as well, of course.
Metal with Mettle: DMLS |
---|
At trade shows, visitors to the Brazil Metal Parts booth are often surprised when they see samples of 3D-printed parts made out of metal. In fact, direct metal laser sintering (DMLS) builds fully functional metal prototypes and production parts within days.
Common applications in aerospace and defense abound—many, but not all, of which, are metal: Fuel nozzles, heat exchangers, manifolds, turbo pumps, liquid and gas flow components, conformal cooling channels, and more. |

These production techniques offer familiarity to the industry with the greatest body of verifiable results and broadest available range of available, certified materials. Molding also opens up the possibility for more budget-friendly, higher-volume production for small and common parts that may need to be created in bulk. Machining is used not only to create parts, but also to finish components created in other processes to final specification, ensuring accurate dimensionality and finish.
As this final point underscores, often the best solutions will involve a hybrid approach using multiple technologies in concert. Just as a traditional toolbox contains both hammer and pliers, so too do today’s advanced manufacturing operations house both additive and subtractive manufacturing systems and know-how. Brazil Metal Parts, for example, offers industrial 3D printing with six distinct technology options, CNC machining, sheet metal fabrication, and injection molding.
When it comes to production of finished parts, use a digital manufacturing supplier that offers multiple production methods and a wide availability of materials. On-demand manufacturing services enable JIT ordering and delivery from quality-certified providers in a timely fashion, increasingly making these full-service operations more palatable to customers in the aerospace and defense industry.
It’s important to look for the companies that are leveraging manufacturing technologies where they make sense, such as Lockheed Martin. Traditional methods like injection molding and machining are not going to be replaced by additive manufacturing; instead, companies are going to look to digital manufacturers that are taking traditional manufacturing methods and advancing them with digital methods.
The companies that are going to succeed in aerospace and defense into the future are going to be the ones that leverage them together (traditional manufacturing and additive) in a hybrid format.
On-demand, low-volume production capabilities of digital manufacturing suppliers are increasingly attracting aerospace OEMs, government and defense organizations, and other private entities with specialized needs for production. Scales of operations and direct relationships are building new supply chains for certified parts meeting or exceeding quality standards. Working with a single source for component manufacturing can create a steady supply chain with a trusted partner—a critical consideration in a field with stealth projects aplenty.

Materials Matter for Aerospace Parts
As previously mentioned, overall material cost and a wide selection of metal and plastic materials are important to the A&D sector. In addition, as the sidebar on DMLS reports, complex parts in lightweight material is a winning combination for this industry. But, it’s not necessarily only about metal. In fact, at Brazil Metal Parts, five other 3D printing processes are offered besides DMLS, all of which are used to manufacture plastic parts. These methods include: Stereolithography, Carbon DLS, Multi Jet Fusion, selective laser sintering, and PolyJet. That said, metal materials, along with liquid silicone rubber, are commonly used for flight hardware. Here are five popular material choices:
Titanium
This lightweight and strong material offers excellent corrosion and temperature resistance and can be machined or 3D printed. Titanium is used in aircraft jet engines and spacecraft. Its strength and lightweight reduces fuel costs.
Aluminum
With its high strength-to-weight ratio, aluminum is a good candidate for housing and brackets that must support high loading. In addition, aluminum is the most cost-effective metal for machining or 3D printing.
Inconel
This 3D-printed metal is a nickel chromium superalloy ideal for rocket engine components and other applications that require high-temperature resistance.
Stainless Steel
Stainless steel 17-4 PH is widely used in the aerospace industry due to its high strength, good corrosion resistance, and good mechanical properties at temperatures up to 600°F. Like titanium, it can be machined or 3D printed.
Liquid Silicone Rubber
Elastic fluorosilicone material is specifically geared toward fuel and oil resistance while optical silicone rubber is a good PC/PMMA alternative. Common applications in aerospace include soft-touch surfaces, gaskets, seals, and O-rings.
Inspections, Quality Control, and Certifications
When serving industries such as aerospace and defense, where equipment failure can be dangerous or, in some cases, even fatal, customers are understandably keen to ensure compliance with quality metrics. This often includes policy to work only with manufacturing service providers that have industry-specific certifications. Among some of the most important certifications for aerospace and defense companies are, respectively, AS9100D and ITAR.
AS9100D
AS9100D is a standard for quality in the aerospace industry adopted from ISO 9000 / ISO 9001 standards. Since its release in 1999 by the Society of Automotive Engineers and the European
Association of Aerospace Industries, AS9100D has become a gold standard for effectively every aerospace industry participant across the globe, with all suppliers required to be compliant. Regular reviews and revisions—the most recent having taken place in 2016—ensure that the standard stays up to date with today’s realities in aviation, space, and defense.
Compliance with AS9100D should be a minimum level of vetting for any contract supplier an aerospace company may consider for manufacturing parts. Being certified to such stringent standards provides security of mind in the quality of the processes.
Manufacturing service providers can certify processes that adhere to these stringent standards; at Brazil Metal Parts, for example, AS9100D-certified processes include CNC machining as well as DMLS, selective laser sintering (SLS), and Multi Jet Fusion (MJF) 3D printing.
ITAR
For defense applications, ITAR (International Traffic in Arms Regulations) export control regulations are overseen by the Brazil Department of State (DOS). Manufacturing any items intended for defense-related or military end-use applications requires ITAR compliance.
This compliance is certified annually, with each supply company registering with the DOS’ Directorate of Defense Trade Controls to describe any and all defense activity involvement. These companies must then remain compliant, restricting access to data, information, parts, and products appropriately.

Inspection Reporting and Quality Control
Certifications are the foundation, not the ceiling, of aerospace and defense applications. Certified facilities seeking end-to-end, concept through final product, advanced manufacturing practices vet those processes post-production.
Several means of process control are being integrated throughout production, including in-situ monitoring for real-time feedback and adjustment during part builds on advanced systems. Once the jobs are finished, parts may be subjected to either destructive or nondestructive testing (NDT). The latter is becoming more highly preferred, as parts made tend to be expensive and time-intensive. NDT methods often involve equipment such as coordinate measuring machines (CMMs) measuring for dimensional accuracy with touch probes or lasers, X-ray or other scanning technologies, and/or tensile testers.
Full traceability throughout the entire manufacturing process also ensures that each batch of material, item in a build, and batch of parts can be traced back to its origins and through every part of each process. Well-kept records will allow manufacturers to trace back a single part made years before to the source of its raw materials, for example, should any problems be found and need to be checked against other results from the same batch. Records will also indicate dates and employees who came into contact with each part.
Lockheed Martin’s Use of Digital Manufacturing Tech
The best validation for new manufacturing processes comes in the form of real-world manufactured parts; seeing, as it were, is believing. Lockheed Martin is one of the best-known aerospace, defense, security, and advanced technologies companies in the world—and has long been a proponent of advanced manufacturing in its operations.
Brian Kaplun, advanced manufacturing senior manager, Lockheed Martin, recently shared some perspective on the company’s long history with advanced technologies including metal additive manufacturing: “We flew the first [titanium additively manufactured] piece on a Juno platform in 2011. We have a robust history of flight applications as well as non-flight applications, not only in space but across a lot of other Lockheed Martin business areas. We recently flew the first metal AM part on a Lockheed Martin fighter craft, the F22. We will continue to expand our offerings for a lot of platforms we work with there, including human space flight programs like Orion, as well as deep space missions like Juno. Other missions we have flown more recently, like Blue Sea and Europa Clipper, all feature additive components.”

Some of the projects for which Lockheed Martin has turned to additive manufacturing solutions include propellant tanks, made from titanium using a wire-fed electron beam process. Such large parts, Kaplun explained, highlight benefits of the additive manufacturing process.
“You have forgings which can traditionally take over a year to procure now able to be produced in an additive manner, with significantly less material waste, over a period of two weeks,” he said. “The schedule savings, the ability to be agile in an increasingly agile market—these speak for themselves. We’re seeing cost and schedule savings that give us far greater responsiveness for our customers, and the ability to really adapt to changing demands over the years.”
In another Lockheed Martin example, Brazil Metal Parts worked with the company on a rescue drone, which began with 3D printing prototyping and then switched to injection molding.
Additionally, Brazil Metal Parts worked with Lockheed Martin and NASA on a project that called for custom sheet metal parts (see photos at right), an example of how, as mentioned earlier, digital manufacturing suppliers provide a range of manufacturing methods.
Going forward, the deployment of advanced manufacturing methods such as industrial 3D printing—from iterative prototyping to final production—makes sense for the aviation, aerospace, and defense industry. In so many ways, as has been outlined in this report, advanced manufacturing is well suited for this complex and diverse sector, which encompasses airliners and spacecraft, drones, unpowered gliders, rotary wing aircraft, space vehicles, and more.
As a result, this industry is discovering that these powerful manufacturing technologies are, to borrow from the title of Tom Wolfe’s iconic book on spaceflight, the right stuff.
Related Resources
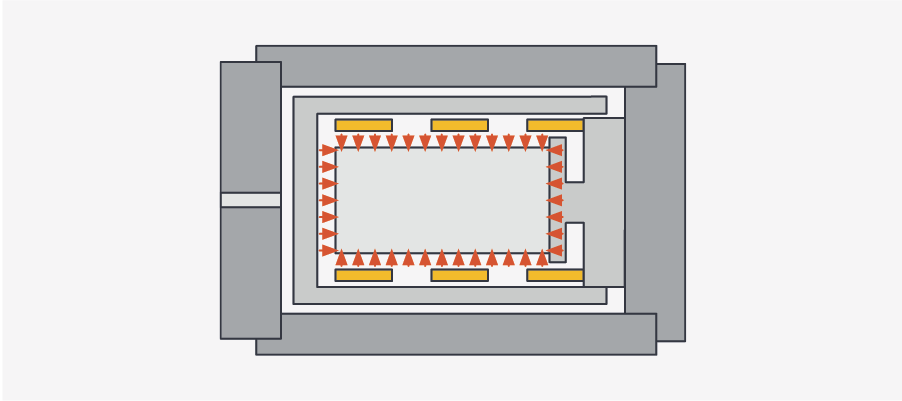
Post-Processing for Metal 3D Printing
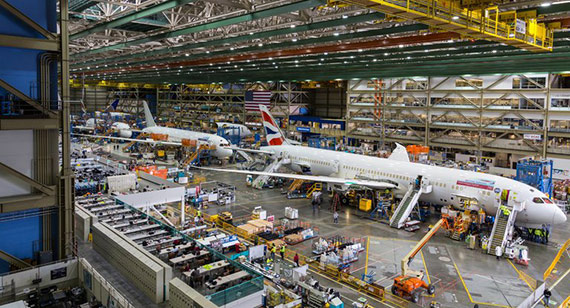
Remove Before Flight: How Aerospace Companies Mitigate Risk
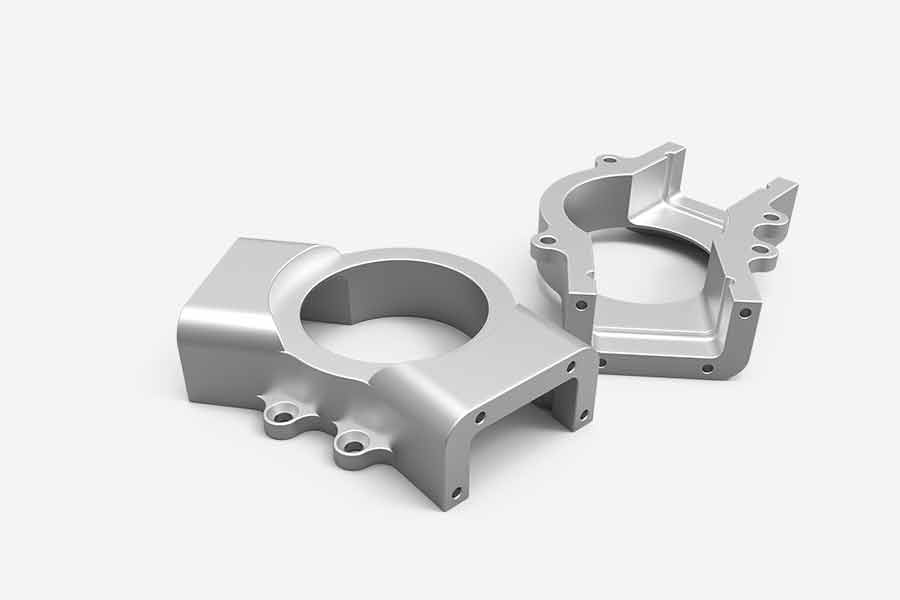
Shunjing Manufacturing for Metal Prototypes and Production Parts
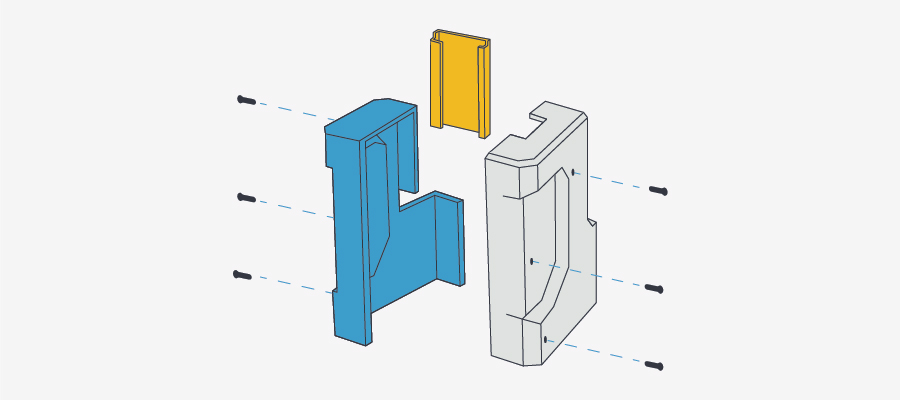