Lightweight Yet Durable Titanium Great Option for Aerospace Parts
The latest post in our Materials Science blog series moves us into the world of machining. Here, we look at high-strength titanium and break down the benefits and weaknesses to help you decide if this is the right material for your next machining project.
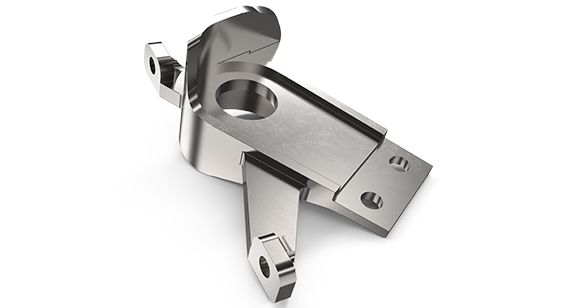
Properties and Specifications
At Brazil Metal Parts we offer titanium material Titanium Grade 5 6Al-4V for metal 3D printing, CNC milling, and CNC turning. This post will focus on the grade 5 alloy used in machining projects. The wrought titanium alloy is the most widely used grade and is a two-phase, Alpha-Beta alloy with aluminum as the alpha stabilizer and vanadium as the beta stabilizer.
Titanium Grade 5 6Al-4V offers very high strength, durability, and corrosion-resistant properties and can be used at a wide array of temperatures from cryogenic (approximately -150 degrees C) all the way to 800 degrees F. These properties make it a good choice for a variety of applications, including fasteners, pressure vessels, and critical forgings requiring high strength-to-weight ratios.
Titanium’s low thermal expansion, with a melting point of around 3,000 degrees F, means it maintains its form well when exposed to heat. The alloy is used in an annealed condition or solution and aged condition, registering 30-34 and 35-39 respectively on the HRC hardness scale. Find more detailed material specifications and comparisons to other metals on the material data sheet from Allegheny Technologies Incorporated published by UL Prospector.
Titanium and the Aerospace Industry
As the 2019 Global Aerospace and Defense Industry Outlook from Deloitte indicates, as upward growth continues to trend for aerospace and defense industries, production demand continues to rise as well. And, when designing for aerospace and defense applications, material selection is critical. For components leaving the earth, component reduction and lightweighting is key. Part designers and engineers in this space know how many ounces of fuel it takes to fly a gram of weight, so slight reductions drive major gains.
The fact that Titanium Grade 5 6Al-4V is light weight, while still offering high strength and temperature resistance, makes it especially popular in the aviation and aerospace industries. Common applications include compressor blades, discs, and rings for jet engines; airframe and space capsule components; rocket engine cases; and helicopter rotor hubs. However, as much as it boasts high temperature and corrosion resistance, titanium is an equally poor electrical conductor, making it a poor option in electrical applications. It is also more expensive compared to other lightweight metals, like aluminum.

Finishing Options Add Extra Resistance
Chromate plating is a great way to protect your titanium machined parts from general wear and tear. And, since grade 5 titanium's appearance varies depending on how much it has been altered, ranging from dull gray in raw form to shiny silver when smooth, plating is a good way to create an enhanced and consistent cosmetic appearance.
Chromate plating is a conversion coating, meaning the process changes the chemical character of the surface, turning it into aluminum oxide. Its protective layer provides corrosion resistance and an improved cosmetic appearance for metal parts. This differs from the anodizing process—available for aluminum parts—in which the part is placed in an acid bath while electricity runs between the metal—acting as a positively charged anode—and the oxygen-rich acid bath. Within the electrical circuit, opposites attract and oxygen bonds to the metal, forming a thicker protective layer on the surface to provide wear and corrosion protection.
For more information on our manufacturing materials, visit our Material Comparison Guide, or order a free CNC machining material selector. The pocket-sized, quick-reference guide helps you identify the right materials for your next project, listing specific measurements on properties to ensure you have the most suitable material and process for your part's application.