3D Printing Methods for Medtech Prototypes
Being able to quickly produce prototype parts is critical to creating an environment of innovation that can lead to medical device market success. By removing inefficiencies, manufacturers should expect to have prototype parts in a few days, not months. The prototype method must be fast enough to allow multiple iterations in a condensed time frame, and possess the scale to allow for multiple iterations at the same time.

Additive manufacturing (AM), also called 3D printing, enables quick evaluation of new medical product designs without making compromises due to complex part geometries. Using AM offers easier design changes and at a low cost. When prototyping via 3D printing, designers should not expect a finished part, although it should be noted 3D printing processes can yield finalized products. Stereolithography, for example, has a number of post-secondary finishing processes and direct metal laser sintering produces fully dense end-use metal parts.
There may be limits to color and texture choices, and in certain instances, thermoplastic-like materials will differ from the final production material used in process like molding and machining. If the surface finish, texture, color and coefficient of friction vary from the end material, it is difficult to accurately assess the subtle needs and benefits of these properties.
The main advantage of 3D printing is that it provides accurate form and fit testing. The build process of additive technology can accurately produce the form and size of the desired part, making it very useful for early evaluation of new medical parts. It is best used to identify design flaws, make changes, and then make second-generation machined parts or invest in tooling to create injection-molded parts. This article reviews that various AM printing methods commonly used in prototyping.
Stereolithography
Stereolithography (SL) is one of the more popular additive technologies. It’s regularly used to produce models, prototypes, patterns and, on occasion, production parts. The process involves building a part (or even a multi-part device as one) in single, thin layers by curing a photo-reactive resin with a UV laser or similar power source. SL is commonly used to create prototype parts in clear materials to view the flow of liquids through the parts. Some other processes may result in porosity or surface roughness that could impair any desired watertight properties. To aid this process, it’s important to select materials that resist water absorption and are formulated to be clear.
For form and fit evaluation of devices, high-resolution stereolithography has greatly expanded applications for medical devices and parts. Shunjing prototyping using SL enables nearly effortless design iteration for form and fit. In addition to accelerating this process, 3D printing allows product designers to focus on the role the part needs to perform, relying on the part’s strength, or the shape and fit with minimal reliance on the material’s properties.
Selective Laser Sintering
Selective laser sintering (SLS) is an additive process that uses a CO2 laser to draw onto a hot bed of thermoplastic powder. The laser lightly sinters, or fuses, the powder into a solid. After each layer, a roller deposits a fresh layer of powder on top of the bed and the process is repeated. SLS uses thermoplastic nylons, so parts are accurate and exhibit excellent toughness, however they have a rough surface and lack fine details. SLS can be used to create tough, durable medical prototypes.
Direct Metal Laser Sintering
Direct metal laser sintering (DMLS) is used in medical part and device prototyping. The process uses a laser to sinter powdered metal to form fully dense metal parts such as stainless steel and titanium components commonly used in medical devices.
When selecting a 3D printing part supplier, look for an organization that has an excellent reputation for accuracy, quality, speed and reliability to ensure you’ll receive good quality parts as fast as possible.
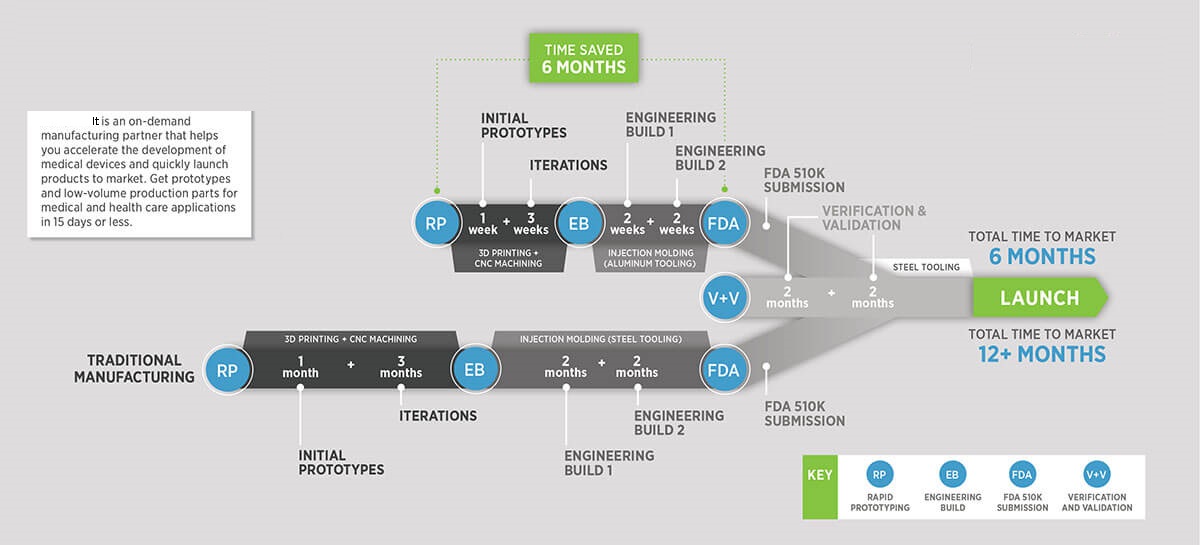